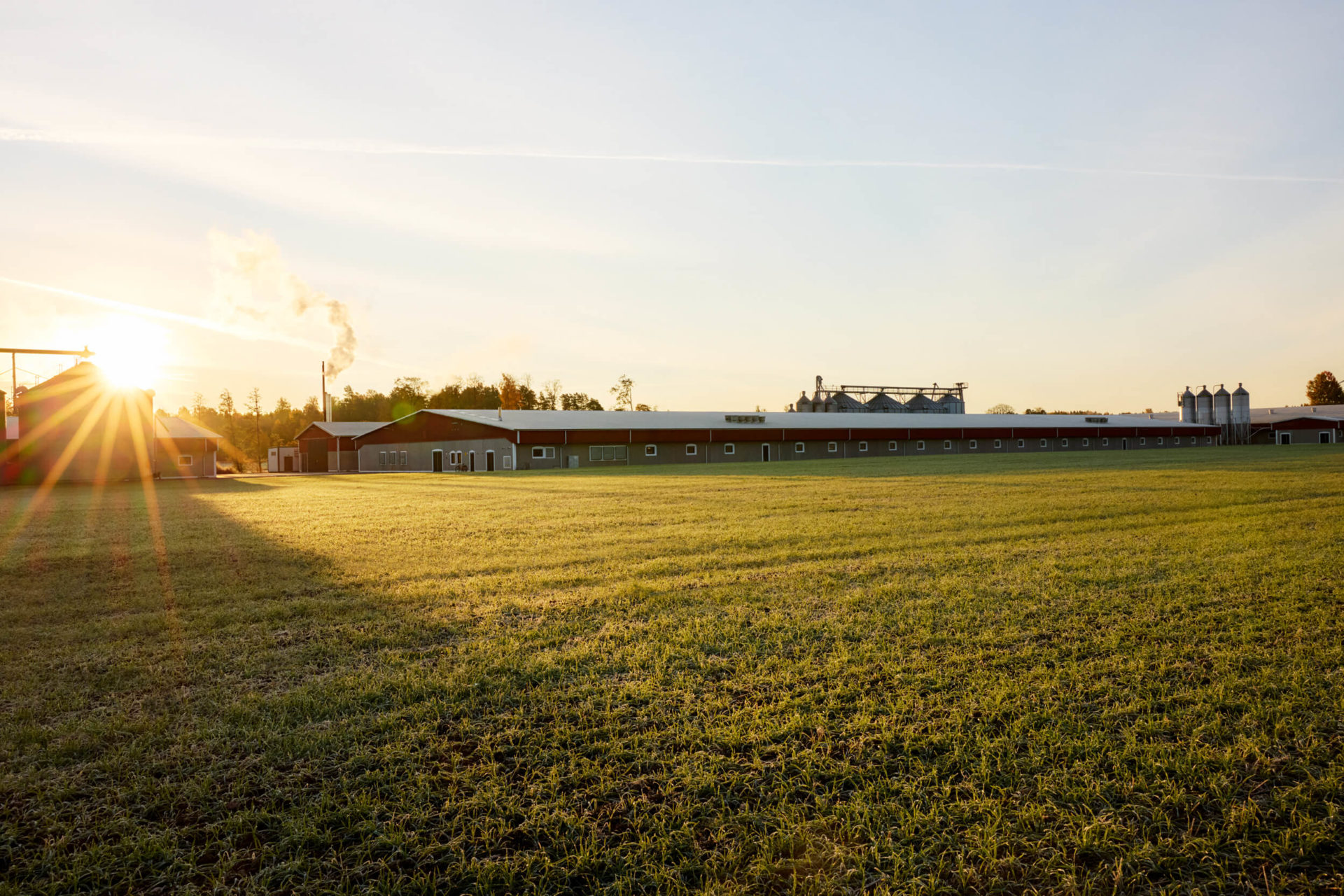
Safe working environment
Most of our employees work in a production environment where there are physical risks associated with health and work safety. Scandi Standard maintains a zero-tolerance approach to occupational accidents and works preventively and systematically on risks related to the physical work environment, as well as the psychosocial work climate and corporate culture. Sick leave and work-related injuries are followed up at each production site and at a Group level. Interim targets are set in every country. These are followed up at each production site, as well as through daily Group Operations debriefings, and on a quarterly basis at the country level and Group level. Each production site conducts regular health and safety training, with a focus on site-specific risks. An important part of health and safety management is regular dialogue between employees and the leadership teams at each production site, for example though health and safety committees.

Health and safety policy
The Group’s policy on health and safety in the workplace clarifies Scandi Standard’s commitment to ensuring a good work environment, to promote health and to ensure compliance with legislation and standards in the area. The policy also mandates active work to ensure an inclusive culture and diversity. Responsibility for implementation of the policy and operational work environment management rests with the relevant company and specific production site. Health and safety management systems include both employees and contractors. Danish operations are certified according to ISO45001, this corresponds to approximately 30 per cent of the Group’s employees or 1076 head counts.
Improvement programme to reduce accidents
Although serious accidents seldom occur, the challenge remains to reduce the total number of accidents. In 2021, the number of work-related injuries resulting in lost time rose, which led to the launch of a Group-wide improvement programme and analysis of the root causes of all the accidents. The aim of the improvement program is to reduce the accident frequency by reinforcing the preventive and systematic management of health and safety.
The focus is on addressing the identified risks at production sites, creating a more robust safety culture and advancing the development of shared working methods and reporting systems. Transparency and clear, consistent KPIs are key elements in the action plan, as are strengthening ownership and local targets.
The improvement programme has yielded results and during the year, the lost time injury frequency rate fell 30 per cent from 39.2 in 2021 to 27.4, in line with the ambitious targets we set early in the year. Work is now ongoing to further improve and strengthen our management of the work environment, by using, for example, a well-defined Group-wide method for reporting and following up near misses.
Read more about our improvement programmeInclusive culture
Scandi Standard aims to be an inclusive organisation that promotes diversity. Our goal is to leverage the potential of all our employees, promote a creative work culture, reflect our customer groups and secure the supply of skills going forward. At Scandi Standard, we respect human rights and show zero tolerance towards discrimination. This is also specified in our Code of Conduct.
Employee satisfaction and inclusivity is measured by our bi-annual survey Scandi Pulse.
Scandi PulseOur employees in numbers
Of all employees in 2022, 43% were women and 57% men. The proportion of women in executive positions, encompassing Group management and the management team of each country was 32%.
Follow-up
• Lost Time Injuries (LTIFR)
• Scandi Pulse – employee satisfaction
• Scandi Pulse – inclusive culture
Milestones 2022
• Lost Time Injuries per million hours worked fell by 30% compared with 2021
• Scandi Pulse conducted and 91% response rate to the employee survey
• 34% women in executive positions